在工業4.0浪潮中,傳統生產線的“剛性”正被柔性制造的靈活性徹底顛覆。面對多品種、小批量、定制化的市場需求,企業亟需能動態響應、高效協同的智能裝備。富唯智能AGV復合機器人以“移動+操作”一體化設計,深度融合導航、機械臂與視覺技術,成為柔性制造場景的破局者。
一、柔性制造核心痛點:從“固定”到“流動”的轉型挑戰
傳統產線依賴固定工位與預設路徑,難以適應訂單波動與工藝迭代。例如,某汽車零部件企業因產品換型需耗時3天調整產線,導致產能損失超百萬元。而柔性制造的核心訴求在于:
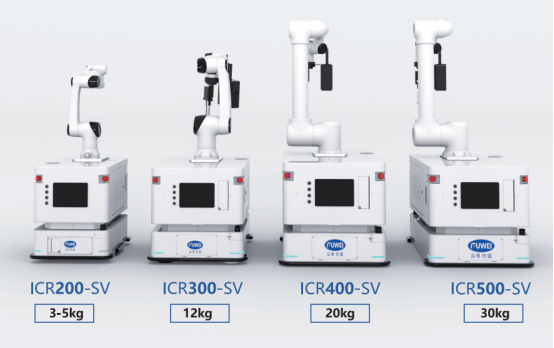
1.快速響應:多任務切換效率提升;
2.動態適應:復雜環境下的自主決策;
3.人機協同:安全靈活的生產單元整合。
富唯智能AGV復合機器人通過三大技術革新,直擊痛點:
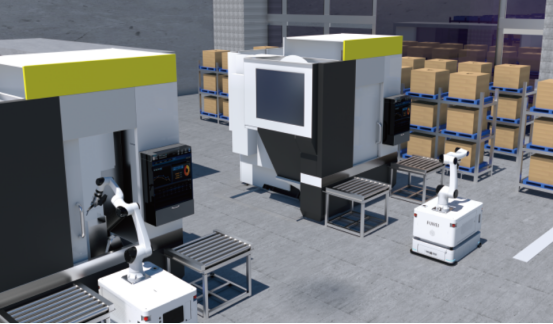
二、技術硬核:富唯智能如何定義柔性制造新標準
1. 模塊化架構,實現“即插即用”柔性升級
“智能積木”設計:機械臂、移動底盤、視覺模塊支持快速拆裝,用戶可根據需求自由組合。例如,某3C電子廠僅用4小時完成從搬運到精密裝配的功能擴展,設備復用率提升70%。
ForwardControl一體化平臺:圖形化拖拽編程,15分鐘配置復雜任務鏈。
?
2. 全向移動+高精度操作,覆蓋全域場景
激光SLAM導航:±5mm定位精度,支持縱向、橫向、斜向及回轉運動,無軌化路徑規劃適應動態車間布局。
±0.05mm作業精度:6軸協作機械臂結合3D視覺系統,可完成微米級精密裝配,良品率提升至99.8%。
?
3. 智能協同,構建“人機共融”生態
動態避障與安全防護:3D避障相機+六維力傳感器,實現0.1秒緊急制動,保障人機協作安全。
集群調度與5G互聯:多臺機器人通過邊緣計算協同作業,產能彈性擴展200%。

三、場景賦能:柔性制造落地實戰案例
案例1:汽車零部件智能產線
某新能源車企引入富唯AGV復合機器人后,實現電池包搬運、螺絲鎖附、質量檢測全流程自動化。柔性制造模式下,產線換型時間從72小時壓縮至8小時,單線日產能提升3倍。
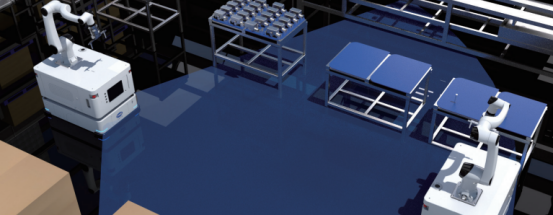
案例2:3C電子精密裝配
在微型元器件裝配中,機器人通過視覺定位精準抓取0.5mm芯片,結合AGV跨工位流轉,生產節拍縮短至45秒,人力成本降低60%。
?
四、未來工廠:柔性制造的價值升維
富唯智能AGV復合機器人不僅是一臺設備,更是柔性制造生態的樞紐:
1.成本優化:模塊化維護使生命周期成本降低50%,投資回報周期縮至18個月4;
2.綠色智造:超長續航與智能功耗管理;
3.數據驅動:生產數據實時上傳MES系統,助力企業精準決策。
在個性化需求主導的時代,富唯智能AGV復合機器人以“技術+場景”雙引擎,重新定義柔性制造的邊界。無論是動態產線重構,還是微米級精密作業,其模塊化、智能化與高兼容性,正推動制造業向更高效、更靈活、更可持續的未來躍進。